Calibração válvula de segurança: funcionamento preciso garantido
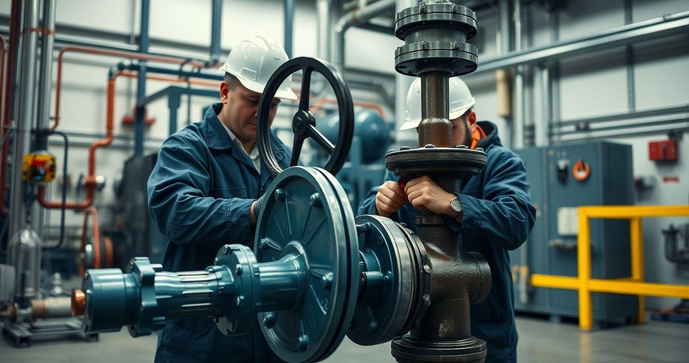
Por: Walter - 28 de Abril de 2025
A calibração de válvula de segurança é um procedimento crucial para garantir a eficiência e a segurança em sistemas industriais. Este processo assegura que as válvulas funcionem corretamente, evitando falhas que podem resultar em acidentes graves. Neste artigo, abordaremos a importância da calibração, o passo a passo para realizá-la, os erros comuns a serem evitados e a necessidade de manutenção regular para garantir a segurança operacional.
Importância da Calibração de Válvula de Segurança para a Segurança Operacional
A calibração de válvula de segurança é um aspecto fundamental na operação de sistemas industriais, especialmente em setores que lidam com substâncias perigosas ou que operam sob alta pressão. Essas válvulas desempenham um papel crucial na proteção de equipamentos e na segurança dos trabalhadores, evitando acidentes que podem resultar em danos materiais e pessoais. Neste contexto, entender a importância da calibração é essencial para garantir a eficiência e a segurança operacional.
As válvulas de segurança são projetadas para abrir automaticamente quando a pressão interna de um sistema atinge níveis críticos, permitindo a liberação de pressão excessiva. Isso evita que o sistema entre em colapso ou que ocorra uma explosão. No entanto, para que essas válvulas funcionem corretamente, é necessário que estejam calibradas de acordo com as especificações do fabricante e as normas de segurança aplicáveis.
Um dos principais motivos para a calibração regular das válvulas de segurança é a prevenção de falhas. Com o tempo, as válvulas podem sofrer desgaste devido a fatores como corrosão, sedimentação e variações de temperatura. Esses fatores podem afetar a capacidade da válvula de abrir e fechar adequadamente, comprometendo sua eficácia. A calibração garante que a válvula responda corretamente às condições de pressão, minimizando o risco de falhas que podem levar a acidentes graves.
Além disso, a calibração de válvula de segurança é uma exigência regulatória em muitos setores. Normas de segurança, como as estabelecidas pela Occupational Safety and Health Administration (OSHA) e pela American Society of Mechanical Engineers (ASME), exigem que as válvulas de segurança sejam testadas e calibradas regularmente. O não cumprimento dessas normas pode resultar em penalidades legais e em riscos à segurança dos trabalhadores. Portanto, a calibração não é apenas uma prática recomendada, mas uma obrigação legal que deve ser levada a sério.
Outro aspecto importante a ser considerado é a eficiência operacional. Válvulas de segurança mal calibradas podem levar a paradas não programadas, resultando em perda de produção e aumento de custos operacionais. Quando uma válvula não abre na pressão correta, pode causar um aumento indesejado na pressão do sistema, levando a interrupções e danos aos equipamentos. A calibração regular ajuda a garantir que as válvulas operem dentro dos parâmetros desejados, contribuindo para a continuidade das operações e a minimização de custos.
Além disso, a calibração de válvula de segurança está diretamente relacionada à segurança dos trabalhadores. Em ambientes industriais, a exposição a pressões excessivas pode resultar em acidentes fatais. A calibração adequada das válvulas de segurança reduz significativamente o risco de acidentes, protegendo não apenas os equipamentos, mas também a vida dos funcionários. Investir na calibração é, portanto, um investimento na segurança e no bem-estar da equipe.
Para garantir a eficácia da calibração, é recomendável utilizar tecnologias avançadas, como o Ultrassom industrial. Essa tecnologia permite a detecção de falhas e a avaliação do desempenho das válvulas de segurança de maneira precisa e eficiente. O uso de ultrassom pode identificar vazamentos e problemas que não são visíveis a olho nu, proporcionando uma análise mais completa do estado das válvulas. Isso não apenas melhora a segurança, mas também otimiza o processo de calibração, tornando-o mais eficaz.
Além disso, a calibração deve ser realizada por profissionais qualificados que compreendam as especificações técnicas das válvulas e as normas de segurança aplicáveis. A falta de conhecimento técnico pode resultar em calibrações inadequadas, comprometendo a segurança operacional. Portanto, é essencial contar com uma equipe treinada e experiente para realizar esse trabalho.
Em resumo, a calibração de válvula de segurança é um componente vital para a segurança operacional em ambientes industriais. Ela previne falhas, atende a exigências regulatórias, melhora a eficiência operacional e protege a vida dos trabalhadores. O uso de tecnologias avançadas, como o ultrassom, pode aprimorar ainda mais esse processo, garantindo que as válvulas funcionem de maneira eficaz e segura. Portanto, investir na calibração regular das válvulas de segurança é uma decisão inteligente e necessária para qualquer operação industrial.
Passo a Passo para Realizar a Calibração de Válvula de Segurança
A calibração de válvulas de segurança é um procedimento essencial para garantir a segurança e a eficiência operacional em sistemas industriais. Realizar essa calibração de forma adequada requer um processo metódico e cuidadoso. A seguir, apresentamos um passo a passo detalhado para a calibração de válvulas de segurança, assegurando que todos os aspectos sejam considerados para um resultado eficaz.
1. Preparação e Planejamento
Antes de iniciar o processo de calibração, é fundamental realizar um planejamento adequado. Isso inclui a coleta de informações sobre a válvula de segurança a ser calibrada, como especificações técnicas, pressão de operação e requisitos do fabricante. Além disso, é importante verificar se todas as ferramentas e equipamentos necessários estão disponíveis, como manômetros, chaves de fenda, e dispositivos de segurança.
Outro aspecto importante da preparação é a análise do ambiente de trabalho. Certifique-se de que a área esteja limpa e livre de obstruções, e que todos os procedimentos de segurança estejam em vigor. Isso inclui o uso de Equipamentos de Proteção Individual (EPIs) adequados, como luvas, óculos de proteção e capacetes, para garantir a segurança dos trabalhadores durante o processo.
2. Desconexão do Sistema
O próximo passo é desconectar a válvula de segurança do sistema em que está instalada. Isso deve ser feito com cuidado, seguindo as diretrizes do fabricante. É importante garantir que não haja pressão residual no sistema antes de desconectar a válvula. Para isso, utilize manômetros para verificar a pressão e, se necessário, ventile o sistema para liberar qualquer pressão acumulada.
Uma vez que a válvula esteja desconectada, é recomendável realizar uma inspeção visual para identificar possíveis danos ou desgastes. Verifique se há corrosão, rachaduras ou outros sinais de deterioração que possam afetar o desempenho da válvula. Se forem encontrados problemas, considere a substituição da válvula antes de prosseguir com a calibração.
3. Montagem do Equipamento de Calibração
Após a inspeção, o próximo passo é montar o equipamento de calibração. Isso geralmente envolve a conexão de um manômetro calibrado à válvula de segurança. O manômetro deve ser capaz de medir a pressão com precisão e deve ser calibrado de acordo com as normas aplicáveis. Certifique-se de que todas as conexões estejam firmes e que não haja vazamentos.
Além disso, é importante garantir que o manômetro esteja posicionado corretamente para obter leituras precisas. A posição do manômetro pode afetar a precisão das medições, portanto, siga as recomendações do fabricante para a instalação.
4. Realização da Calibração
Com o equipamento montado, é hora de realizar a calibração. Comece aumentando a pressão gradualmente no sistema até atingir a pressão de abertura especificada para a válvula de segurança. Durante esse processo, observe atentamente o manômetro para garantir que a pressão esteja sendo aumentada de forma controlada e segura.
Quando a pressão de abertura for alcançada, verifique se a válvula se abre corretamente. A válvula deve abrir e liberar a pressão conforme projetado. Se a válvula não abrir na pressão correta, será necessário ajustar a configuração da válvula de acordo com as especificações do fabricante. Isso pode envolver a rotação de um parafuso de ajuste ou a modificação de outros componentes da válvula.
Após a calibração inicial, é importante realizar um teste de fechamento. Reduza a pressão gradualmente e verifique se a válvula fecha adequadamente. A válvula deve ser capaz de selar completamente, evitando vazamentos. Se houver vazamentos, a válvula pode precisar de manutenção adicional ou substituição.
5. Documentação e Registro
Uma vez que a calibração tenha sido concluída com sucesso, é essencial documentar todo o processo. Registre as leituras de pressão, os ajustes realizados e quaisquer observações relevantes. Essa documentação é importante para garantir a conformidade com as normas de segurança e para futuras referências.
Além disso, a documentação pode ser necessária para auditorias e inspeções, como as Inspeções nr13, que exigem que as válvulas de segurança sejam testadas e calibradas regularmente. Manter registros precisos ajuda a garantir que a empresa esteja em conformidade com as regulamentações e que a segurança operacional seja mantida.
6. Reinstalação e Testes Finais
Após a calibração e a documentação, a válvula de segurança pode ser reinstalada no sistema. Certifique-se de que todas as conexões estejam firmes e que não haja vazamentos. Após a reinstalação, é recomendável realizar testes finais para garantir que a válvula funcione corretamente dentro do sistema. Isso inclui verificar se a válvula abre e fecha conforme esperado sob condições de operação normais.
Além disso, é importante programar calibrações regulares para garantir que a válvula de segurança continue a operar de forma eficaz ao longo do tempo. A manutenção preventiva é fundamental para evitar falhas e garantir a segurança operacional.
Em resumo, a calibração de válvulas de segurança é um processo crítico que deve ser realizado com cuidado e atenção aos detalhes. Seguir este passo a passo ajuda a garantir que as válvulas funcionem corretamente, protegendo tanto os equipamentos quanto a segurança dos trabalhadores. Investir tempo e recursos na calibração adequada é uma decisão inteligente que pode prevenir acidentes e garantir a eficiência operacional em ambientes industriais.
Erros Comuns na Calibração de Válvula de Segurança e Como Evitá-los
A calibração de válvulas de segurança é um procedimento crítico para garantir a segurança e a eficiência operacional em sistemas industriais. No entanto, erros podem ocorrer durante esse processo, comprometendo a eficácia das válvulas e colocando em risco a segurança dos trabalhadores e a integridade dos equipamentos. Neste artigo, abordaremos os erros comuns na calibração de válvulas de segurança e como evitá-los, assegurando que o processo seja realizado de maneira eficaz.
1. Falta de Preparação Adequada
Um dos erros mais frequentes na calibração de válvulas de segurança é a falta de preparação adequada. Isso inclui não coletar informações suficientes sobre a válvula, como suas especificações técnicas e requisitos de calibração. Antes de iniciar o processo, é fundamental revisar o manual do fabricante e entender as características da válvula, como a pressão de abertura e fechamento.
Para evitar esse erro, é recomendável criar uma lista de verificação que inclua todos os passos necessários para a calibração, bem como as ferramentas e equipamentos que serão utilizados. Além disso, certifique-se de que todos os membros da equipe estejam cientes do procedimento e das responsabilidades de cada um durante o processo.
2. Uso de Equipamentos Não Calibrados
Outro erro comum é o uso de equipamentos de calibração que não estão devidamente calibrados. Manômetros e outros dispositivos de medição devem ser verificados regularmente para garantir que estão funcionando corretamente. Se um manômetro estiver descalibrado, as leituras podem ser imprecisas, levando a ajustes inadequados na válvula de segurança.
Para evitar esse problema, é essencial realizar a Calibração de manometros regularmente e manter registros precisos das calibrações realizadas. Além disso, sempre verifique a calibração dos equipamentos antes de iniciar o processo de calibração da válvula de segurança.
3. Ignorar a Inspeção Visual
A inspeção visual da válvula de segurança antes da calibração é um passo crucial que muitas vezes é negligenciado. Ignorar essa etapa pode resultar em falhas não detectadas que podem comprometer a eficácia da válvula. Danos, corrosão ou obstruções podem afetar o desempenho da válvula e levar a resultados imprecisos durante a calibração.
Para evitar esse erro, sempre realize uma inspeção visual detalhada antes de iniciar a calibração. Verifique se há sinais de desgaste, corrosão ou danos físicos. Se forem encontrados problemas, considere a substituição da válvula antes de prosseguir com a calibração.
4. Pressão de Abertura Incorreta
Um erro comum na calibração de válvulas de segurança é não ajustar a pressão de abertura corretamente. Cada válvula tem uma pressão de abertura específica que deve ser respeitada. Se a pressão de abertura for ajustada incorretamente, a válvula pode não abrir quando necessário, colocando em risco a segurança do sistema.
Para evitar esse erro, consulte sempre as especificações do fabricante e ajuste a pressão de abertura de acordo com as diretrizes. Utilize manômetros calibrados para garantir que a pressão esteja sendo medida com precisão. Além disso, é recomendável realizar testes de abertura e fechamento após a calibração para verificar se a válvula está funcionando corretamente.
5. Falta de Documentação
A documentação adequada é essencial para garantir a conformidade com as normas de segurança e para futuras referências. Um erro comum é não registrar as leituras de pressão, os ajustes realizados e quaisquer observações relevantes durante o processo de calibração. A falta de documentação pode dificultar a identificação de problemas futuros e comprometer a segurança operacional.
Para evitar esse erro, mantenha registros detalhados de cada calibração realizada. Isso deve incluir informações sobre a válvula, as condições de calibração, as leituras de pressão e quaisquer ajustes feitos. A documentação não apenas ajuda a garantir a conformidade com as normas, mas também fornece um histórico valioso para futuras calibrações e inspeções.
6. Não Realizar Testes Finais
Após a calibração, é fundamental realizar testes finais para garantir que a válvula de segurança esteja funcionando corretamente. Um erro comum é não realizar esses testes, o que pode resultar em falhas não detectadas. Testes de abertura e fechamento devem ser realizados para verificar se a válvula responde adequadamente às condições de operação.
Para evitar esse erro, sempre inclua testes finais como parte do processo de calibração. Verifique se a válvula abre e fecha na pressão correta e se não há vazamentos. Esses testes são essenciais para garantir que a válvula esteja pronta para operar de forma segura e eficaz.
7. Ignorar a Manutenção Preventiva
A calibração de válvulas de segurança não deve ser vista como uma tarefa única, mas sim como parte de um programa de manutenção preventiva contínua. Ignorar a manutenção regular pode levar a falhas e comprometer a segurança do sistema. É importante programar calibrações regulares e inspeções para garantir que as válvulas estejam sempre em boas condições de funcionamento.
Para evitar esse erro, desenvolva um cronograma de manutenção que inclua calibrações regulares, inspeções visuais e testes de desempenho. Isso ajudará a garantir que as válvulas de segurança operem de forma eficaz e que quaisquer problemas sejam identificados e corrigidos antes que se tornem críticos.
Em resumo, a calibração de válvulas de segurança é um processo complexo que requer atenção aos detalhes e um planejamento cuidadoso. Evitar erros comuns, como falta de preparação, uso de equipamentos não calibrados e ignorar a inspeção visual, é fundamental para garantir a eficácia das válvulas e a segurança operacional. Ao seguir as melhores práticas e manter registros precisos, as empresas podem minimizar riscos e garantir que suas válvulas de segurança funcionem de maneira confiável.
Manutenção e Verificação Regular da Válvula de Segurança após a Calibração
A manutenção e verificação regular das válvulas de segurança são essenciais para garantir que esses dispositivos funcionem corretamente e continuem a proteger os sistemas industriais ao longo do tempo. Após a calibração, é fundamental implementar um programa de manutenção que inclua inspeções periódicas, testes de desempenho e a utilização de tecnologias avançadas para garantir a integridade das válvulas. Neste artigo, discutiremos a importância da manutenção e verificação regular das válvulas de segurança, bem como as melhores práticas para garantir sua eficácia.
1. Importância da Manutenção Regular
A manutenção regular das válvulas de segurança é crucial para prevenir falhas e garantir a segurança operacional. Com o tempo, as válvulas podem sofrer desgaste devido a fatores como corrosão, sedimentação e variações de temperatura. Esses fatores podem afetar a capacidade da válvula de abrir e fechar adequadamente, comprometendo sua eficácia. A manutenção regular ajuda a identificar e corrigir problemas antes que se tornem críticos, garantindo que as válvulas funcionem conforme projetado.
Além disso, a manutenção regular é uma exigência regulatória em muitos setores. Normas de segurança, como as estabelecidas pela Occupational Safety and Health Administration (OSHA) e pela American Society of Mechanical Engineers (ASME), exigem que as válvulas de segurança sejam inspecionadas e testadas periodicamente. O não cumprimento dessas normas pode resultar em penalidades legais e em riscos à segurança dos trabalhadores.
2. Inspeções Visuais
Uma das primeiras etapas na manutenção das válvulas de segurança é realizar inspeções visuais regulares. Essas inspeções devem ser feitas para verificar se há sinais de desgaste, corrosão ou danos físicos. Durante a inspeção, é importante observar se há vazamentos, rachaduras ou obstruções que possam afetar o desempenho da válvula.
As inspeções visuais devem ser realizadas com uma frequência adequada, dependendo das condições de operação e do ambiente em que a válvula está instalada. Em ambientes agressivos, como aqueles com alta umidade ou exposição a produtos químicos, as inspeções podem precisar ser mais frequentes. Documentar os resultados das inspeções é fundamental para manter um histórico e identificar tendências ao longo do tempo.
3. Testes de Desempenho
Além das inspeções visuais, é essencial realizar testes de desempenho regulares nas válvulas de segurança. Esses testes devem incluir a verificação da pressão de abertura e fechamento, bem como a capacidade da válvula de selar adequadamente. Os testes devem ser realizados em condições controladas para garantir resultados precisos.
Durante os testes, é importante utilizar manômetros calibrados e equipamentos de medição adequados. Se a válvula não abrir ou fechar na pressão correta, ajustes devem ser feitos imediatamente. Além disso, é recomendável realizar testes de vazamento para garantir que a válvula esteja funcionando corretamente e não apresente falhas.
4. Uso de Tecnologias Avançadas
Para otimizar a manutenção e verificação das válvulas de segurança, muitas empresas estão adotando tecnologias avançadas, como o Ensaio não destrutivo ultrassom. Essa tecnologia permite a detecção de falhas e a avaliação do desempenho das válvulas de segurança de maneira precisa e eficiente. O uso de ultrassom pode identificar vazamentos e problemas que não são visíveis a olho nu, proporcionando uma análise mais completa do estado das válvulas.
O ensaio não destrutivo ultrassom é uma técnica que utiliza ondas sonoras para detectar falhas internas e externas nas válvulas. Essa abordagem é especialmente útil em ambientes industriais, onde a segurança é uma prioridade. A implementação de tecnologias como o ultrassom não apenas melhora a segurança, mas também otimiza o processo de manutenção, tornando-o mais eficaz e menos dispendioso.
5. Registro e Documentação
Manter registros detalhados de todas as atividades de manutenção e verificação é fundamental para garantir a conformidade com as normas de segurança e para futuras referências. Os registros devem incluir informações sobre as inspeções visuais, os testes de desempenho realizados, os ajustes feitos e quaisquer observações relevantes.
A documentação não apenas ajuda a garantir a conformidade com as normas, mas também fornece um histórico valioso para futuras calibrações e inspeções. Além disso, manter registros precisos pode ser útil durante auditorias e inspeções regulatórias, demonstrando que a empresa está comprometida com a segurança e a manutenção adequada de suas válvulas de segurança.
6. Treinamento da Equipe
Um aspecto muitas vezes negligenciado na manutenção de válvulas de segurança é o treinamento da equipe responsável por realizar as inspeções e testes. É fundamental que os profissionais envolvidos no processo de manutenção estejam devidamente treinados e capacitados para identificar problemas e realizar ajustes adequados.
Investir em treinamento contínuo para a equipe não apenas melhora a eficácia da manutenção, mas também aumenta a segurança operacional. A equipe deve estar ciente das melhores práticas, das normas de segurança e das técnicas de calibração e verificação. Isso garante que todos os procedimentos sejam realizados de maneira correta e eficiente.
7. Programação de Manutenção Preventiva
Por fim, é essencial desenvolver um cronograma de manutenção preventiva que inclua inspeções regulares, testes de desempenho e a utilização de tecnologias avançadas. A programação de manutenção deve ser baseada nas recomendações do fabricante, nas condições de operação e nas normas de segurança aplicáveis.
Um cronograma bem estruturado ajuda a garantir que as válvulas de segurança sejam mantidas em boas condições de funcionamento e que quaisquer problemas sejam identificados e corrigidos antes que se tornem críticos. A manutenção preventiva é uma estratégia eficaz para minimizar riscos e garantir a segurança operacional em ambientes industriais.
Em resumo, a manutenção e verificação regular das válvulas de segurança após a calibração são essenciais para garantir a segurança e a eficiência operacional. Implementar um programa de manutenção que inclua inspeções visuais, testes de desempenho, uso de tecnologias avançadas, documentação adequada e treinamento da equipe é fundamental para garantir que as válvulas funcionem de maneira eficaz e segura ao longo do tempo. Investir na manutenção regular é uma decisão inteligente que pode prevenir acidentes e garantir a integridade dos sistemas industriais.
Em conclusão, a calibração de válvula de segurança é um elemento vital para a operação segura e eficiente de sistemas industriais. Através de um processo metódico que inclui a preparação adequada, a realização de testes de desempenho e a manutenção regular, é possível garantir que as válvulas funcionem conforme projetado, minimizando riscos e prevenindo acidentes. Além disso, a conscientização sobre os erros comuns e a implementação de tecnologias avançadas, como o ensaio não destrutivo, podem otimizar ainda mais a eficácia das válvulas. Investir na calibração e na manutenção contínua não apenas atende às exigências regulatórias, mas também protege a vida dos trabalhadores e a integridade dos equipamentos, assegurando um ambiente de trabalho seguro e produtivo.