Calibração de manômetros: garanta medições confiáveis
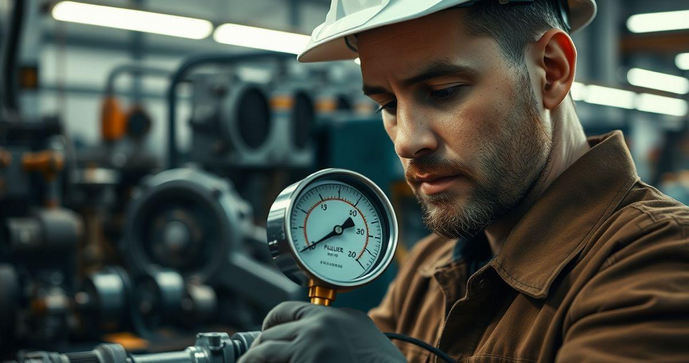
Por: Walter - 28 de Abril de 2025
A calibração de manômetros é um processo fundamental para garantir a precisão e a confiabilidade das medições em diversos setores, como industrial e laboratorial. Com o uso adequado, esses instrumentos podem evitar falhas operacionais e garantir a segurança dos processos. Neste artigo, abordaremos a importância da calibração, os métodos utilizados, a frequência recomendada e os erros comuns que devem ser evitados durante esse procedimento.
Importância da Calibração de Manômetros na Indústria
A calibração de manômetros é um aspecto crucial na manutenção da precisão e confiabilidade dos instrumentos de medição utilizados na indústria. Esses dispositivos são responsáveis por medir a pressão de gases e líquidos em diversos processos, e sua precisão é vital para garantir a segurança e a eficiência operacional. A seguir, discutiremos a importância da calibração de manômetros e como ela impacta diretamente a qualidade e a segurança das operações industriais.
Um dos principais motivos para a calibração de manômetros é a necessidade de garantir medições precisas. Em ambientes industriais, pequenas variações na pressão podem resultar em consequências significativas, como falhas em equipamentos, acidentes de trabalho e até mesmo danos ao produto final. Por exemplo, em processos de fabricação de produtos químicos, a pressão inadequada pode levar a reações indesejadas, comprometendo a qualidade do produto e colocando em risco a segurança dos trabalhadores.
Além disso, a calibração regular dos manômetros é essencial para atender às normas e regulamentações de segurança. Muitas indústrias são obrigadas a seguir padrões rigorosos estabelecidos por órgãos reguladores, que exigem a verificação periódica da precisão dos instrumentos de medição. A não conformidade com essas normas pode resultar em penalidades financeiras, interrupções na produção e danos à reputação da empresa. Portanto, a calibração não é apenas uma prática recomendada, mas uma exigência legal em muitos casos.
Outro aspecto importante da calibração de manômetros é a redução de custos operacionais. Instrumentos de medição imprecisos podem levar a decisões erradas, como a utilização excessiva de recursos, desperdício de materiais e aumento do tempo de inatividade. Por exemplo, se um manômetro estiver descalibrado e indicar uma pressão mais baixa do que a real, pode-se acabar utilizando mais energia para compensar essa diferença, resultando em custos adicionais. A calibração regular ajuda a evitar esses problemas, garantindo que os manômetros funcionem de maneira eficiente e econômica.
A calibração também desempenha um papel fundamental na manutenção da qualidade do produto. Em setores como alimentos e bebidas, farmacêuticos e petroquímicos, a precisão das medições de pressão é vital para garantir que os produtos atendam aos padrões de qualidade exigidos. Um manômetro descalibrado pode resultar em produtos fora das especificações, levando a rejeições, retrabalhos e até mesmo recalls. Portanto, a calibração é uma prática que não apenas protege a segurança dos trabalhadores, mas também assegura a qualidade do produto final.
Além disso, a calibração de manômetros contribui para a longevidade dos equipamentos. Instrumentos que não são calibrados regularmente podem sofrer desgaste prematuro e falhas mecânicas. A pressão inadequada pode causar danos aos componentes internos do manômetro, resultando em custos adicionais com reparos e substituições. Ao realizar a calibração de forma sistemática, as empresas podem identificar problemas potenciais antes que se tornem críticos, prolongando a vida útil dos equipamentos e reduzindo a necessidade de manutenção corretiva.
Outro ponto a ser considerado é a integração da calibração de manômetros com outras tecnologias de medição. Com o avanço da tecnologia, muitos setores estão adotando soluções de automação e monitoramento em tempo real. A calibração de manômetros deve ser parte integrante dessas soluções, garantindo que os dados coletados sejam precisos e confiáveis. Por exemplo, sistemas de Ultrassom industrial podem ser utilizados em conjunto com manômetros para monitorar a pressão em tempo real, permitindo ajustes imediatos e melhorando a eficiência operacional.
Por fim, a calibração de manômetros é uma prática que promove a cultura de segurança dentro das organizações. Ao priorizar a calibração e a manutenção de instrumentos de medição, as empresas demonstram um compromisso com a segurança dos trabalhadores e a qualidade dos produtos. Isso não apenas melhora a moral da equipe, mas também fortalece a reputação da empresa no mercado, atraindo clientes que valorizam a segurança e a qualidade.
Em resumo, a calibração de manômetros é de extrema importância na indústria, pois garante medições precisas, atende a normas de segurança, reduz custos operacionais, mantém a qualidade do produto, prolonga a vida útil dos equipamentos e promove uma cultura de segurança. As empresas que investem na calibração regular de seus manômetros não apenas protegem seus trabalhadores e produtos, mas também asseguram a eficiência e a competitividade no mercado.
Métodos Comuns de Calibração de Manômetros
A calibração de manômetros é um processo essencial para garantir a precisão e a confiabilidade das medições de pressão em diversos setores industriais. Existem vários métodos de calibração que podem ser utilizados, cada um com suas características e aplicações específicas. Neste artigo, abordaremos os métodos mais comuns de calibração de manômetros, destacando suas vantagens e desvantagens, além de considerar a importância de seguir as normas e regulamentos, como as Inspeções nr13.
Um dos métodos mais tradicionais de calibração de manômetros é o uso de um manômetro de referência. Este método envolve a comparação do manômetro a ser calibrado com um manômetro de alta precisão, que serve como padrão. O manômetro de referência é conectado ao mesmo ponto de medição que o manômetro a ser calibrado, e ambos são submetidos a uma série de pressões conhecidas. As leituras dos dois manômetros são comparadas, e qualquer discrepância é registrada. Este método é eficaz e amplamente utilizado, mas requer que o manômetro de referência esteja sempre calibrado e em boas condições de funcionamento.
Outro método comum é a calibração por meio de um calibrador de pressão. Os calibradores de pressão são dispositivos projetados especificamente para medir e ajustar a pressão de manômetros. Eles podem ser manuais ou eletrônicos e são capazes de gerar pressões conhecidas com alta precisão. O manômetro a ser calibrado é conectado ao calibrador, e a pressão é ajustada para os pontos de calibração desejados. Este método é vantajoso porque permite uma calibração rápida e precisa, além de ser mais fácil de usar em comparação com o método de referência. No entanto, é importante garantir que o calibrador também esteja calibrado e mantenha sua precisão.
A calibração por comparação é outro método utilizado, especialmente em ambientes onde a precisão extrema não é crítica. Neste método, o manômetro a ser calibrado é comparado a um manômetro de referência em um intervalo de pressão específico. As leituras são registradas e, se necessário, ajustes são feitos. Este método é mais simples e pode ser realizado rapidamente, mas pode não ser tão preciso quanto os métodos anteriores. É ideal para aplicações onde a precisão não é a principal preocupação, mas ainda assim é importante garantir que as medições estejam dentro de limites aceitáveis.
Além dos métodos mencionados, a calibração de manômetros também pode ser realizada utilizando um sistema de pressão de gás ou líquido. Neste método, um sistema de pressão é criado utilizando um gás ou líquido de referência, e o manômetro a ser calibrado é conectado a esse sistema. A pressão é ajustada e as leituras são comparadas. Este método é útil em situações onde a calibração precisa ser realizada em campo, pois não requer equipamentos de laboratório sofisticados. No entanto, é importante garantir que o sistema de pressão esteja bem controlado para evitar variações que possam afetar a precisão das medições.
Outro método que tem ganhado popularidade é a calibração digital, que utiliza tecnologia avançada para realizar medições e ajustes. Os manômetros digitais modernos frequentemente possuem recursos de auto-calibração, que permitem que o próprio dispositivo ajuste suas leituras com base em padrões internos. Essa tecnologia pode ser extremamente útil em ambientes industriais, onde a rapidez e a precisão são essenciais. No entanto, é importante que os usuários compreendam como a tecnologia funciona e que realizem verificações regulares para garantir que o sistema esteja operando corretamente.
Independentemente do método escolhido, a calibração de manômetros deve ser realizada em intervalos regulares, conforme recomendado pelos fabricantes e pelas normas de segurança. A frequência da calibração pode variar dependendo do tipo de manômetro, da aplicação e das condições de operação. Por exemplo, manômetros utilizados em ambientes críticos, como indústrias químicas ou farmacêuticas, podem exigir calibrações mais frequentes do que aqueles utilizados em aplicações menos exigentes.
Além disso, é fundamental que a calibração seja realizada por profissionais qualificados, que compreendam os princípios de medição e as normas aplicáveis. A calibração inadequada pode resultar em medições imprecisas, comprometendo a segurança e a eficiência das operações. Portanto, investir em treinamento e certificação para a equipe responsável pela calibração é uma prática recomendada.
Em resumo, a calibração de manômetros é um processo vital que pode ser realizado por meio de diversos métodos, incluindo comparação com manômetros de referência, uso de calibradores de pressão, calibração por comparação e sistemas de pressão. Cada método possui suas vantagens e desvantagens, e a escolha do método adequado dependerá das necessidades específicas da aplicação. A calibração regular e adequada é essencial para garantir a precisão das medições e a conformidade com as normas de segurança, como as Inspeções nr13, assegurando a segurança e a eficiência nas operações industriais.
Frequência Recomendada para Calibração de Manômetros
A calibração de manômetros é um processo essencial para garantir a precisão e a confiabilidade das medições de pressão em diversos setores industriais. No entanto, a eficácia desse processo depende não apenas da técnica utilizada, mas também da frequência com que a calibração é realizada. Neste artigo, discutiremos a frequência recomendada para a calibração de manômetros, considerando fatores como tipo de aplicação, ambiente de operação e normas regulatórias.
Em geral, a frequência de calibração de manômetros pode variar de acordo com a indústria e a aplicação específica. Para manômetros utilizados em ambientes críticos, como indústrias químicas, farmacêuticas e petroquímicas, a calibração deve ser realizada com mais frequência. Nesses setores, onde a precisão das medições é vital para a segurança e a qualidade do produto, recomenda-se que a calibração ocorra a cada seis meses ou até mesmo trimestralmente. Isso garante que os instrumentos estejam sempre dentro das especificações e que qualquer desvio seja corrigido rapidamente.
Por outro lado, em aplicações menos críticas, como em ambientes de manufatura geral, a frequência de calibração pode ser estendida. Nesses casos, a calibração pode ser realizada anualmente ou a cada dois anos, dependendo das condições de operação e do histórico de desempenho do manômetro. É importante ressaltar que, mesmo em aplicações menos exigentes, a calibração regular é fundamental para evitar problemas futuros e garantir a precisão das medições.
Outro fator a ser considerado na determinação da frequência de calibração é o ambiente em que o manômetro está operando. Manômetros expostos a condições adversas, como temperaturas extremas, umidade elevada ou vibrações, podem sofrer desgastes mais rapidamente e, portanto, podem exigir calibrações mais frequentes. Por exemplo, em ambientes industriais onde há variações bruscas de temperatura, a calibração pode precisar ser realizada a cada três meses para garantir que os instrumentos permaneçam precisos.
Além disso, a frequência de calibração também pode ser influenciada pelo tipo de manômetro utilizado. Manômetros analógicos, por exemplo, podem ser mais suscetíveis a desgastes e variações em suas leituras ao longo do tempo, enquanto manômetros digitais modernos podem ter recursos de auto-calibração que permitem uma maior estabilidade nas medições. Portanto, é importante considerar as especificações do fabricante e as recomendações para cada tipo de manômetro ao determinar a frequência de calibração.
As normas regulatórias também desempenham um papel importante na definição da frequência de calibração. Muitas indústrias são obrigadas a seguir normas específicas que estabelecem requisitos de calibração para instrumentos de medição. Por exemplo, a norma ISO 9001, que trata da gestão da qualidade, recomenda que a calibração de instrumentos de medição seja realizada em intervalos regulares, conforme especificado pelo fabricante ou por normas aplicáveis. Além disso, normas específicas, como as Calibração de manometros da NR-13, podem exigir calibrações mais frequentes para garantir a segurança em sistemas de pressão.
É importante ressaltar que a calibração não deve ser vista apenas como uma obrigação regulatória, mas como uma prática que contribui para a eficiência operacional e a segurança. A calibração regular ajuda a identificar problemas potenciais antes que se tornem críticos, evitando falhas operacionais e garantindo a qualidade do produto final. Além disso, a calibração adequada pode resultar em economia de custos, uma vez que manômetros imprecisos podem levar a desperdícios de materiais e energia.
Para garantir que a calibração seja realizada de forma eficaz, é recomendável que as empresas mantenham um registro detalhado das calibrações realizadas, incluindo datas, resultados e quaisquer ajustes feitos. Esses registros não apenas ajudam a monitorar a frequência de calibração, mas também podem ser úteis em auditorias e inspeções. Além disso, a documentação adequada pode servir como um histórico valioso para a análise de desempenho dos manômetros ao longo do tempo.
Por fim, é fundamental que a calibração seja realizada por profissionais qualificados e treinados, que compreendam os princípios de medição e as normas aplicáveis. A calibração inadequada pode resultar em medições imprecisas, comprometendo a segurança e a eficiência das operações. Portanto, investir em treinamento e certificação para a equipe responsável pela calibração é uma prática recomendada.
Em resumo, a frequência recomendada para a calibração de manômetros varia de acordo com a aplicação, o ambiente de operação e as normas regulatórias. Manômetros utilizados em ambientes críticos devem ser calibrados com mais frequência, enquanto aqueles em aplicações menos exigentes podem ter intervalos mais longos. A calibração regular é essencial para garantir a precisão das medições, a conformidade com as normas e a segurança nas operações industriais. Ao seguir as diretrizes adequadas e manter registros detalhados, as empresas podem assegurar que seus manômetros estejam sempre operando de maneira eficiente e confiável.
Erros Comuns na Calibração de Manômetros e Como Evitá-los
A calibração de manômetros é um processo crítico para garantir a precisão e a confiabilidade das medições de pressão em diversas aplicações industriais. No entanto, existem erros comuns que podem ocorrer durante esse processo, comprometendo a eficácia da calibração e, consequentemente, a segurança e a eficiência das operações. Neste artigo, discutiremos os erros mais frequentes na calibração de manômetros e como evitá-los.
Um dos erros mais comuns é a falta de um manômetro de referência calibrado. A calibração deve ser realizada em comparação com um instrumento de alta precisão, que serve como padrão. Se o manômetro de referência não estiver calibrado ou não for adequado para a faixa de pressão do manômetro a ser calibrado, as medições podem ser imprecisas. Para evitar esse erro, é fundamental garantir que o manômetro de referência esteja sempre em conformidade com as normas de calibração e que seja verificado regularmente. Além disso, é importante utilizar um manômetro de referência que tenha uma faixa de medição compatível com o manômetro a ser calibrado.
Outro erro comum é a calibração em condições inadequadas. A temperatura, a umidade e a pressão atmosférica podem afetar as medições de pressão. Realizar a calibração em um ambiente que não esteja controlado pode resultar em leituras imprecisas. Para evitar esse problema, é recomendável realizar a calibração em um ambiente controlado, onde as condições possam ser monitoradas e mantidas dentro dos limites especificados pelo fabricante. Além disso, é importante permitir que os instrumentos se aclimatizem à temperatura do ambiente antes de iniciar o processo de calibração.
A falta de um procedimento de calibração padronizado também pode levar a erros. Cada tipo de manômetro pode ter requisitos específicos para a calibração, e seguir um procedimento inadequado pode resultar em medições imprecisas. Para evitar esse erro, as empresas devem desenvolver e documentar procedimentos de calibração claros e detalhados, que incluam etapas específicas a serem seguidas, intervalos de calibração e critérios de aceitação. Esses procedimentos devem ser revisados e atualizados regularmente para garantir que estejam em conformidade com as melhores práticas e normas aplicáveis.
Outro erro frequente é a falta de treinamento adequado para os profissionais responsáveis pela calibração. A calibração de manômetros requer conhecimento técnico e habilidades específicas. Profissionais não treinados podem cometer erros durante o processo, resultando em medições imprecisas. Para evitar esse problema, as empresas devem investir em treinamento e certificação para sua equipe de calibração. Isso não apenas melhora a precisão das medições, mas também promove uma cultura de segurança e qualidade dentro da organização.
A calibração inadequada dos manômetros também pode ocorrer devido à falta de manutenção regular. Manômetros que não são mantidos adequadamente podem apresentar desgastes e falhas que afetam suas medições. É importante realizar inspeções regulares e manutenção preventiva nos manômetros, incluindo a verificação de conexões, vedações e componentes internos. Além disso, a documentação das manutenções realizadas pode ajudar a identificar padrões de desgaste e a necessidade de calibrações mais frequentes.
Outro erro comum é a não realização de testes de verificação após a calibração. Após calibrar um manômetro, é fundamental realizar testes para garantir que ele esteja funcionando corretamente e que as medições estejam dentro das especificações. Ignorar essa etapa pode resultar em problemas não detectados que podem comprometer a segurança e a eficiência das operações. Para evitar esse erro, as empresas devem incluir testes de verificação como parte do procedimento de calibração, garantindo que os manômetros estejam operando corretamente antes de serem colocados de volta em serviço.
Além disso, a falta de registros adequados de calibração pode ser um erro significativo. Manter registros detalhados das calibrações realizadas, incluindo datas, resultados e ajustes feitos, é essencial para monitorar o desempenho dos manômetros ao longo do tempo. Esses registros não apenas ajudam a garantir a conformidade com as normas, mas também podem ser úteis em auditorias e inspeções. Para evitar esse problema, as empresas devem implementar um sistema de gerenciamento de registros que facilite o acompanhamento das calibrações e manutenções realizadas.
Por fim, é importante considerar a integração da calibração de manômetros com outras tecnologias de medição. A utilização de sistemas avançados, como o Ensaio não destrutivo ultrassom, pode complementar a calibração e fornecer dados adicionais sobre o desempenho dos manômetros. A combinação de diferentes métodos de medição pode aumentar a precisão e a confiabilidade das medições, reduzindo a probabilidade de erros.
Em resumo, a calibração de manômetros é um processo crítico que pode ser comprometido por erros comuns, como a falta de um manômetro de referência calibrado, condições inadequadas de calibração, ausência de procedimentos padronizados, falta de treinamento, manutenção inadequada, não realização de testes de verificação e falta de registros. Ao identificar e evitar esses erros, as empresas podem garantir a precisão das medições, a conformidade com as normas e a segurança nas operações industriais. Investir em treinamento, documentação e procedimentos adequados é fundamental para promover a qualidade e a eficiência na calibração de manômetros.
A calibração de manômetros é um aspecto essencial para a manutenção da precisão e confiabilidade nas medições de pressão, impactando diretamente a segurança e a eficiência das operações industriais. Ao compreender a importância desse processo, os métodos disponíveis, a frequência recomendada e os erros comuns a serem evitados, as empresas podem implementar práticas eficazes que garantam a qualidade de seus produtos e a segurança de seus colaboradores. Investir em calibração regular e em treinamento adequado para a equipe responsável é fundamental para minimizar riscos e maximizar a eficiência operacional, assegurando que os manômetros funcionem de maneira ideal em todas as circunstâncias.