Calibração de manômetros: como garantir precisão nas medições
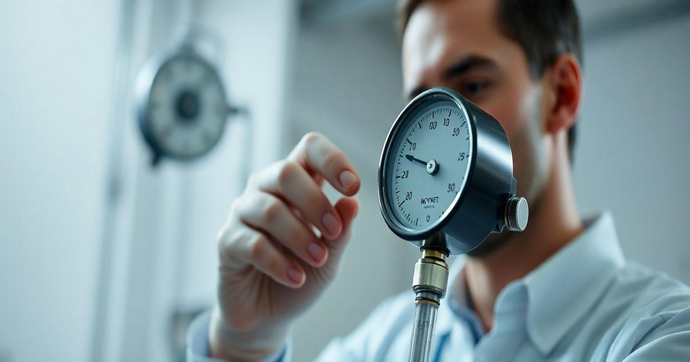
Por: Walter - 16 de Janeiro de 2025
A calibração de manômetros é um processo fundamental para garantir a precisão e a confiabilidade das medições em diversos setores, como industrial, laboratorial e de engenharia. Com o uso adequado desses instrumentos, é possível evitar erros que podem comprometer a segurança e a eficiência dos processos. Neste artigo, abordaremos a importância da calibração, os tipos de manômetros disponíveis, os procedimentos recomendados e os benefícios de manter esses equipamentos sempre calibrados.
1. Importância da Calibração de Manômetros na Indústria
A calibração de manômetros é um aspecto crucial na operação de diversos setores industriais, pois esses instrumentos são responsáveis por medir a pressão de gases e líquidos em sistemas variados. A precisão dessas medições é vital para garantir a segurança, a eficiência e a qualidade dos processos produtivos. Neste contexto, a calibração regular dos manômetros se torna uma prática indispensável para evitar falhas e garantir a conformidade com normas e regulamentos.
Um dos principais motivos para a calibração de manômetros é a segurança. Em indústrias que lidam com substâncias perigosas, como produtos químicos ou gases inflamáveis, uma medição imprecisa pode resultar em acidentes graves, como explosões ou vazamentos. A calibração assegura que os manômetros estejam funcionando corretamente, permitindo que os operadores identifiquem rapidamente qualquer anomalia no sistema. Isso é especialmente importante em setores como o petroquímico, farmacêutico e de alimentos, onde a segurança dos trabalhadores e a integridade dos produtos são prioridades.
Além da segurança, a calibração de manômetros também impacta diretamente a eficiência operacional. Medições imprecisas podem levar a decisões erradas, como ajustes inadequados nas pressões de operação, resultando em desperdício de recursos e aumento de custos. Por exemplo, em uma planta de produção, se a pressão de um sistema não estiver calibrada corretamente, pode haver um consumo excessivo de energia ou a necessidade de manutenção mais frequente dos equipamentos. Isso não apenas afeta a produtividade, mas também pode comprometer a rentabilidade da empresa.
A qualidade do produto final é outro fator que depende da calibração adequada dos manômetros. Em indústrias onde a pressão é um parâmetro crítico, como na fabricação de bebidas ou na produção de medicamentos, a precisão das medições é essencial para garantir que os produtos atendam aos padrões de qualidade estabelecidos. A calibração regular ajuda a evitar variações que podem resultar em produtos fora das especificações, o que pode levar a retrabalhos, desperdícios e insatisfação do cliente.
Além disso, a calibração de manômetros é uma exigência regulatória em muitos setores. Normas e regulamentações, como as estabelecidas pela ISO e pela ANVISA, frequentemente exigem que os instrumentos de medição sejam calibrados em intervalos regulares. O não cumprimento dessas normas pode resultar em penalidades, multas e até mesmo a suspensão das operações. Portanto, manter um programa de calibração eficaz não é apenas uma questão de boa prática, mas também uma necessidade legal.
Outro aspecto importante a ser considerado é a vida útil dos manômetros. Instrumentos que não são calibrados regularmente podem sofrer desgastes e falhas, levando à necessidade de substituição prematura. A calibração ajuda a identificar problemas antes que se tornem críticos, permitindo que as empresas realizem manutenções preventivas e prolonguem a vida útil dos equipamentos. Isso não apenas reduz os custos com a compra de novos manômetros, mas também minimiza o tempo de inatividade dos sistemas.
Para garantir a eficácia da calibração, é fundamental que as empresas adotem práticas de diligenciamento e sigam procedimentos padronizados. Isso inclui a escolha de laboratórios de calibração acreditados, que utilizam equipamentos de alta precisão e seguem normas reconhecidas. Além disso, é importante documentar todas as calibrações realizadas, mantendo registros que possam ser utilizados em auditorias e inspeções.
Em resumo, a calibração de manômetros é uma prática essencial na indústria, que impacta diretamente a segurança, a eficiência operacional, a qualidade do produto e a conformidade regulatória. As empresas que investem em programas de calibração eficazes não apenas protegem seus trabalhadores e ativos, mas também garantem a satisfação do cliente e a sustentabilidade de suas operações. Portanto, é fundamental que a calibração seja encarada como uma prioridade e não como uma tarefa secundária, assegurando que os manômetros estejam sempre prontos para fornecer medições precisas e confiáveis.
2. Tipos de Manômetros e Suas Aplicações
Os manômetros são instrumentos essenciais para a medição de pressão em diversos setores industriais. Existem diferentes tipos de manômetros, cada um projetado para atender a necessidades específicas e condições de operação. Neste artigo, exploraremos os principais tipos de manômetros e suas aplicações, destacando a importância de escolher o instrumento adequado para cada situação.
Um dos tipos mais comuns de manômetros é o manômetro de tubo Bourdon. Este dispositivo utiliza um tubo curvado que se desdobra quando a pressão interna aumenta. O movimento do tubo é convertido em um movimento de ponteiro, que indica a pressão em uma escala. Os manômetros de tubo Bourdon são amplamente utilizados em indústrias como a petroquímica, onde a medição de pressão é crucial para a segurança e a eficiência dos processos. Eles são conhecidos por sua robustez e capacidade de medir pressões elevadas, tornando-os ideais para aplicações em ambientes exigentes.
Outro tipo popular é o manômetro digital, que fornece leituras de pressão em formato numérico. Esses manômetros são frequentemente utilizados em laboratórios e aplicações de precisão, onde a exatidão é fundamental. Os manômetros digitais podem incluir recursos adicionais, como alarmes e registros de dados, permitindo que os usuários monitorem as pressões ao longo do tempo. Sua facilidade de leitura e a capacidade de fornecer medições em tempo real os tornam uma escolha preferida em muitas indústrias, incluindo farmacêutica e alimentícia.
Os manômetros de pressão diferencial são projetados para medir a diferença de pressão entre dois pontos. Eles são frequentemente utilizados em sistemas de ventilação e climatização, onde é importante monitorar a pressão em diferentes seções do sistema. Esses manômetros ajudam a garantir que os sistemas estejam funcionando de maneira eficiente e que não haja obstruções que possam comprometer o desempenho. Além disso, são utilizados em processos industriais que requerem controle preciso da pressão, como em reatores químicos.
Os manômetros de coluna de líquido, como os manômetros de mercúrio ou água, são instrumentos tradicionais que utilizam a altura de uma coluna de líquido para medir a pressão. Embora menos comuns em aplicações modernas devido a preocupações com a toxicidade do mercúrio, esses manômetros ainda são utilizados em algumas indústrias, especialmente em laboratórios de pesquisa. Eles são conhecidos por sua precisão e simplicidade, mas requerem cuidados especiais na manipulação e descarte do líquido utilizado.
Os manômetros de pressão absoluta são projetados para medir a pressão em relação ao vácuo absoluto. Eles são essenciais em aplicações onde a pressão deve ser monitorada em relação a um ambiente de vácuo, como em processos de fabricação de semicondutores e em sistemas de vácuo em laboratórios. Esses manômetros garantem que as medições sejam precisas, independentemente das variações na pressão atmosférica.
Além dos tipos mencionados, existem manômetros específicos para aplicações em alta temperatura e alta pressão, como os manômetros de diafragma. Esses instrumentos são projetados para suportar condições extremas e são frequentemente utilizados em indústrias químicas e petroquímicas. O diafragma flexível permite que o manômetro meça a pressão sem ser afetado por temperaturas elevadas ou pela corrosão de fluidos agressivos.
A escolha do tipo de manômetro adequado depende de vários fatores, incluindo a faixa de pressão a ser medida, o ambiente de operação e a precisão necessária. É fundamental considerar as especificações do processo e as condições em que o manômetro será utilizado. Além disso, a calibração regular é essencial para garantir que os manômetros continuem a fornecer medições precisas ao longo do tempo.
As Inspeções nr13 são um exemplo de regulamentação que exige a utilização de manômetros adequados e calibrados em sistemas de vapor e pressão. Essas inspeções garantem que os equipamentos estejam em conformidade com as normas de segurança e operem de maneira eficiente, minimizando riscos e garantindo a integridade dos processos industriais.
Em resumo, a variedade de tipos de manômetros disponíveis no mercado permite que as indústrias escolham o instrumento mais adequado para suas necessidades específicas. Desde manômetros de tubo Bourdon até manômetros digitais e de pressão diferencial, cada tipo tem suas próprias características e aplicações. A escolha correta do manômetro, juntamente com a calibração regular, é fundamental para garantir medições precisas e confiáveis, contribuindo para a segurança e a eficiência dos processos industriais.
3. Procedimentos para Calibração de Manômetros
A calibração de manômetros é um processo essencial para garantir a precisão e a confiabilidade das medições de pressão em diversos setores industriais. A seguir, apresentaremos os principais procedimentos para a calibração de manômetros, destacando a importância de seguir um protocolo adequado para assegurar resultados precisos e consistentes.
O primeiro passo na calibração de manômetros é a preparação do equipamento. Antes de iniciar o processo, é fundamental verificar se o manômetro está em boas condições de funcionamento. Isso inclui a inspeção visual do instrumento, procurando por danos físicos, corrosão ou vazamentos. Qualquer anomalia deve ser corrigida antes de prosseguir com a calibração. Além disso, é importante garantir que o manômetro esteja limpo e livre de sujeira, pois contaminantes podem afetar a precisão das medições.
Após a verificação inicial, o próximo passo é escolher um padrão de referência adequado. A calibração deve ser realizada utilizando um manômetro de referência que tenha uma precisão superior ao manômetro que está sendo calibrado. Esse padrão de referência pode ser um manômetro calibrado em laboratório ou um instrumento de calibração especializado. A escolha do padrão é crucial, pois a precisão do manômetro calibrado dependerá da qualidade do padrão utilizado.
Uma vez que o padrão de referência foi selecionado, o manômetro a ser calibrado deve ser conectado ao sistema de calibração. Isso geralmente envolve a utilização de um conjunto de conexões e adaptadores que garantam uma vedação adequada e evitem vazamentos. É importante seguir as instruções do fabricante para a conexão correta dos instrumentos, garantindo que não haja perda de pressão durante o processo de calibração.
Com o manômetro conectado, o próximo passo é aplicar pressões conhecidas ao sistema. Isso pode ser feito utilizando um gerador de pressão, que permite ajustar a pressão de forma precisa e controlada. O manômetro a ser calibrado deve ser exposto a uma série de pressões, que abrangem toda a sua faixa de medição. Durante esse processo, as leituras do manômetro calibrado devem ser registradas e comparadas com as leituras do padrão de referência.
É importante realizar múltiplas medições em cada ponto de pressão para garantir a consistência dos resultados. A média das leituras pode ser utilizada para calcular a precisão do manômetro calibrado em relação ao padrão de referência. Caso as leituras apresentem discrepâncias significativas, pode ser necessário ajustar o manômetro, se ele tiver essa capacidade, ou considerar a necessidade de reparos ou substituição.
Após a calibração, é fundamental documentar todos os resultados obtidos. A documentação deve incluir as pressões aplicadas, as leituras do manômetro calibrado e as leituras do padrão de referência. Além disso, é importante registrar a data da calibração, o nome do técnico responsável e qualquer observação relevante. Essa documentação é essencial para auditorias e para garantir a rastreabilidade das medições.
Outro aspecto importante a ser considerado é a frequência de calibração. A calibração de manômetros deve ser realizada em intervalos regulares, que podem variar de acordo com o tipo de manômetro, a aplicação e as recomendações do fabricante. Em geral, manômetros utilizados em ambientes críticos ou que operam sob condições severas devem ser calibrados com mais frequência. A implementação de um programa de calibração de manômetros eficaz ajuda a garantir que todos os instrumentos estejam sempre em conformidade e funcionando corretamente.
Além da calibração regular, é importante realizar inspeções periódicas nos manômetros. Essas inspeções podem incluir verificações visuais, testes de funcionalidade e avaliações de desempenho. A identificação precoce de problemas pode evitar falhas graves e garantir que os manômetros continuem a fornecer medições precisas ao longo do tempo.
Por fim, é recomendável que a calibração de manômetros seja realizada por profissionais qualificados e treinados. Técnicos experientes têm o conhecimento necessário para seguir os procedimentos corretos e garantir que a calibração seja realizada de forma adequada. Além disso, eles podem identificar problemas que podem não ser evidentes para operadores não treinados, garantindo a integridade do processo de calibração.
Em resumo, a calibração de manômetros é um processo crítico que envolve a preparação do equipamento, a escolha de padrões de referência, a aplicação de pressões conhecidas e a documentação dos resultados. Seguir esses procedimentos de forma rigorosa é essencial para garantir a precisão e a confiabilidade das medições de pressão, contribuindo para a segurança e a eficiência das operações industriais.
4. Erros Comuns na Calibração e Como Evitá-los
A calibração de manômetros é um processo crítico para garantir a precisão das medições de pressão em diversos setores industriais. No entanto, existem erros comuns que podem comprometer a eficácia desse processo. Neste artigo, abordaremos os principais erros na calibração de manômetros e como evitá-los, assegurando que os instrumentos funcionem corretamente e forneçam resultados confiáveis.
Um dos erros mais frequentes na calibração de manômetros é a falta de preparação adequada do equipamento. Antes de iniciar o processo de calibração, é essencial realizar uma inspeção visual do manômetro. Isso inclui verificar se há danos físicos, corrosão ou vazamentos. Ignorar essa etapa pode resultar em medições imprecisas e até mesmo em falhas no equipamento. Para evitar esse erro, sempre faça uma verificação completa do manômetro antes de conectá-lo ao sistema de calibração.
Outro erro comum é a escolha inadequada do padrão de referência. A calibração deve ser realizada utilizando um manômetro de referência que tenha uma precisão superior ao manômetro que está sendo calibrado. Se o padrão de referência não for adequado, as medições do manômetro calibrado podem ser comprometidas. Para evitar esse problema, sempre verifique as especificações do padrão de referência e assegure-se de que ele esteja calibrado e em boas condições de funcionamento.
Durante o processo de calibração, a aplicação de pressões conhecidas é uma etapa crucial. Um erro comum é não aplicar uma faixa de pressões que abranja toda a capacidade do manômetro. Se as pressões aplicadas não forem representativas da faixa de operação do manômetro, as medições podem não refletir com precisão o desempenho do instrumento. Para evitar esse erro, sempre aplique pressões em toda a faixa de medição do manômetro, realizando múltiplas medições em cada ponto para garantir a consistência dos resultados.
Além disso, a falta de documentação adequada durante a calibração é um erro que pode ter consequências sérias. A documentação deve incluir as pressões aplicadas, as leituras do manômetro calibrado e as do padrão de referência, além de informações sobre o técnico responsável e a data da calibração. A ausência de registros pode dificultar auditorias e comprometer a rastreabilidade das medições. Para evitar esse problema, sempre mantenha registros detalhados de cada calibração realizada, garantindo que todas as informações relevantes sejam documentadas.
Outro erro que pode ocorrer é a calibração em condições inadequadas. Fatores como temperatura, umidade e vibração podem afetar as medições de pressão. Realizar a calibração em um ambiente que não esteja dentro das especificações recomendadas pode resultar em resultados imprecisos. Para evitar esse erro, sempre realize a calibração em um ambiente controlado, onde as condições possam ser monitoradas e mantidas dentro dos limites aceitáveis.
Além disso, a falta de treinamento adequado dos técnicos responsáveis pela calibração é um erro que pode comprometer a qualidade do processo. Técnicos não treinados podem não seguir os procedimentos corretos, resultando em medições imprecisas. Para evitar esse problema, é fundamental que os profissionais envolvidos na calibração recebam treinamento adequado e estejam atualizados sobre as melhores práticas e procedimentos recomendados.
Outro aspecto a ser considerado é a contaminação do sistema de calibração. A presença de partículas magnéticas ou outros contaminantes pode afetar a precisão das medições. É importante garantir que todos os componentes do sistema de calibração estejam limpos e livres de contaminantes antes de iniciar o processo. Para evitar esse erro, sempre realize uma limpeza adequada dos equipamentos e verifique se não há obstruções que possam interferir nas medições.
Por fim, a falta de manutenção regular dos manômetros e do equipamento de calibração pode levar a erros significativos. Instrumentos que não são mantidos adequadamente podem apresentar falhas que afetam a precisão das medições. Para evitar esse problema, implemente um programa de manutenção regular que inclua inspeções e calibrações periódicas, garantindo que todos os instrumentos estejam sempre em boas condições de funcionamento.
Em resumo, a calibração de manômetros é um processo que requer atenção a detalhes e a adoção de boas práticas. Evitar erros comuns, como a falta de preparação do equipamento, a escolha inadequada do padrão de referência, a aplicação de pressões limitadas, a falta de documentação, a calibração em condições inadequadas, a falta de treinamento, a contaminação do sistema e a falta de manutenção, é fundamental para garantir a precisão e a confiabilidade das medições. Ao seguir essas diretrizes, as empresas podem assegurar que seus manômetros funcionem corretamente e contribuam para a segurança e a eficiência das operações industriais.
5. Frequência Recomendada para Calibração de Manômetros
A calibração de manômetros é uma prática essencial para garantir a precisão e a confiabilidade das medições de pressão em diversos setores industriais. No entanto, a frequência com que essa calibração deve ser realizada pode variar dependendo de vários fatores, incluindo o tipo de manômetro, a aplicação, as condições de operação e as recomendações do fabricante. Neste artigo, discutiremos a frequência recomendada para a calibração de manômetros e os fatores que influenciam essa decisão.
Em geral, a calibração de manômetros deve ser realizada em intervalos regulares para garantir que os instrumentos continuem a fornecer medições precisas. A frequência recomendada pode variar de mensal a anual, dependendo das condições de uso. Por exemplo, manômetros utilizados em ambientes críticos ou que operam sob condições severas, como altas temperaturas ou pressões extremas, podem exigir calibrações mais frequentes. Em contrapartida, manômetros que são utilizados em condições mais estáveis podem ser calibrados com menos frequência.
Um dos principais fatores a considerar ao determinar a frequência de calibração é a aplicação do manômetro. Em indústrias onde a precisão é crucial, como na farmacêutica ou na alimentícia, a calibração deve ser realizada com mais frequência. Isso se deve ao fato de que pequenas variações nas medições podem ter um impacto significativo na qualidade do produto final. Portanto, é recomendável que as empresas que operam nesses setores implementem um programa de calibração rigoroso, com intervalos mais curtos entre as calibrações.
Outro fator a ser considerado é a idade do manômetro. Instrumentos mais antigos podem apresentar um desempenho inferior em comparação com modelos mais novos, e sua precisão pode deteriorar-se com o tempo. Por isso, manômetros mais antigos podem exigir calibrações mais frequentes para garantir que continuem a operar dentro das especificações. Além disso, se um manômetro foi submetido a condições adversas, como choques mecânicos ou exposição a substâncias corrosivas, a calibração deve ser realizada imediatamente após esses eventos.
A utilização de manômetros em ambientes onde há vibrações constantes ou mudanças bruscas de temperatura também pode afetar a precisão das medições. Nesses casos, é aconselhável realizar calibrações mais frequentes para garantir que os instrumentos estejam sempre em conformidade. A vibração pode causar desgaste nas partes internas do manômetro, enquanto as mudanças de temperatura podem afetar a dilatação dos materiais, resultando em medições imprecisas.
Além disso, as recomendações do fabricante devem ser sempre consideradas ao determinar a frequência de calibração. Muitos fabricantes fornecem diretrizes específicas sobre a frequência recomendada para a calibração de seus produtos. Essas diretrizes são baseadas em testes e experiências acumuladas ao longo do tempo e devem ser seguidas para garantir o desempenho ideal do manômetro. Portanto, é importante consultar o manual do fabricante e seguir suas recomendações para a calibração.
Outra prática recomendada é a realização de calibrações periódicas, mesmo que não haja sinais de falha no manômetro. Isso é especialmente importante em indústrias onde a segurança é uma preocupação primordial. A calibração regular ajuda a identificar problemas antes que se tornem críticos, permitindo que as empresas realizem manutenções preventivas e evitem falhas que possam resultar em acidentes ou interrupções nas operações.
Além da calibração regular, é importante realizar inspeções periódicas nos manômetros. Essas inspeções podem incluir verificações visuais, testes de funcionalidade e avaliações de desempenho. A identificação precoce de problemas pode evitar falhas graves e garantir que os manômetros continuem a fornecer medições precisas ao longo do tempo.
Em resumo, a frequência recomendada para a calibração de manômetros varia de acordo com vários fatores, incluindo a aplicação, as condições de operação, a idade do instrumento e as recomendações do fabricante. Implementar um programa de calibração eficaz, que inclua intervalos regulares e inspeções periódicas, é fundamental para garantir a precisão e a confiabilidade das medições de pressão. Ao seguir essas diretrizes, as empresas podem assegurar que seus manômetros funcionem corretamente e contribuam para a segurança e a eficiência das operações industriais.
6. Benefícios da Calibração Regular para a Precisão das Medições
A calibração regular de manômetros é uma prática essencial que traz uma série de benefícios significativos para a precisão das medições de pressão em diversos setores industriais. A seguir, discutiremos os principais benefícios da calibração regular, destacando como essa prática contribui para a eficiência operacional, a segurança e a qualidade dos produtos.
Um dos principais benefícios da calibração regular é a garantia de medições precisas. Com o tempo, os manômetros podem sofrer desgastes e variações em seu desempenho, o que pode levar a medições imprecisas. A calibração regular ajuda a identificar e corrigir essas discrepâncias, assegurando que os instrumentos forneçam leituras confiáveis. Isso é especialmente importante em indústrias onde a precisão é crucial, como na farmacêutica e na alimentícia, onde pequenas variações nas medições podem ter um impacto significativo na qualidade do produto final.
Além de garantir a precisão, a calibração regular também contribui para a segurança operacional. Em indústrias que lidam com substâncias perigosas, como produtos químicos ou gases inflamáveis, a precisão das medições de pressão é vital para evitar acidentes. Um manômetro impreciso pode resultar em pressões inadequadas, levando a vazamentos, explosões ou outras falhas catastróficas. A calibração regular ajuda a minimizar esses riscos, garantindo que os manômetros estejam sempre funcionando dentro das especificações de segurança.
Outro benefício importante da calibração regular é a melhoria da eficiência operacional. Manômetros imprecisos podem levar a decisões erradas, como ajustes inadequados nas pressões de operação, resultando em desperdício de recursos e aumento de custos. Por exemplo, se um manômetro não estiver calibrado corretamente, pode haver um consumo excessivo de energia ou a necessidade de manutenção mais frequente dos equipamentos. A calibração regular ajuda a evitar esses problemas, permitindo que as empresas operem de maneira mais eficiente e econômica.
A calibração regular também desempenha um papel fundamental na conformidade regulatória. Muitas indústrias são obrigadas a seguir normas e regulamentações que exigem a calibração de instrumentos de medição em intervalos específicos. O não cumprimento dessas normas pode resultar em penalidades, multas e até mesmo a suspensão das operações. Ao implementar um programa de calibração regular, as empresas garantem que estão em conformidade com as regulamentações aplicáveis, evitando problemas legais e financeiros.
Além disso, a calibração regular contribui para a durabilidade dos manômetros. Instrumentos que não são calibrados regularmente podem sofrer desgastes e falhas, levando à necessidade de substituição prematura. A calibração ajuda a identificar problemas antes que se tornem críticos, permitindo que as empresas realizem manutenções preventivas e prolonguem a vida útil dos equipamentos. Isso não apenas reduz os custos com a compra de novos manômetros, mas também minimiza o tempo de inatividade dos sistemas.
Outro aspecto importante é a melhoria da qualidade do produto final. Em indústrias onde a pressão é um parâmetro crítico, a precisão das medições é essencial para garantir que os produtos atendam aos padrões de qualidade estabelecidos. A calibração regular ajuda a evitar variações que podem resultar em produtos fora das especificações, o que pode levar a retrabalhos, desperdícios e insatisfação do cliente. Ao garantir medições precisas, as empresas podem melhorar a qualidade de seus produtos e aumentar a satisfação do cliente.
Além disso, a calibração regular pode ajudar a identificar tendências e padrões de desempenho ao longo do tempo. Ao registrar os resultados das calibrações, as empresas podem monitorar o desempenho dos manômetros e identificar quaisquer problemas recorrentes. Isso permite que as empresas tomem medidas proativas para resolver problemas antes que se tornem críticos, melhorando ainda mais a eficiência e a confiabilidade dos sistemas de medição.
Por fim, a calibração regular promove uma cultura de qualidade e segurança dentro da organização. Ao priorizar a calibração e a manutenção dos manômetros, as empresas demonstram seu compromisso com a precisão, a segurança e a qualidade. Isso pode resultar em uma maior conscientização entre os funcionários sobre a importância das medições precisas e da manutenção adequada, promovendo um ambiente de trabalho mais seguro e eficiente.
Em resumo, a calibração regular de manômetros oferece uma série de benefícios significativos, incluindo a garantia de medições precisas, a melhoria da segurança operacional, a eficiência, a conformidade regulatória, a durabilidade dos equipamentos, a qualidade do produto final e a promoção de uma cultura de qualidade. Implementar um programa de calibração regular é fundamental para garantir que os manômetros funcionem corretamente e contribuam para a segurança e a eficiência das operações industriais.
Em conclusão, a calibração de manômetros é uma prática essencial que não apenas assegura a precisão das medições, mas também contribui para a segurança e a eficiência operacional em diversos setores. Através da compreensão da importância da calibração, dos diferentes tipos de manômetros e dos procedimentos adequados, as empresas podem implementar estratégias eficazes para manter seus instrumentos em conformidade e funcionando corretamente. Os benefícios de uma calibração regular, como a melhoria da qualidade do produto, a conformidade regulatória e a durabilidade dos equipamentos, reforçam a necessidade de priorizar essa prática. Ao investir na calibração de manômetros, as organizações garantem um ambiente de trabalho mais seguro e eficiente, promovendo a confiança em suas operações e resultados.